- Explore our industry expertise
- Success stories
- Data visualisation platform saves an estimated of $100 million over 4 years
Data visualisation platform saves an estimated of $100 million over 4 years

Data becomes a factor of production
Trucks and equipment are more reliable with fewer failures and less downtime
Investment aligned with quantifiable benefits
Maintenance budgets are lower and can be accurately forecast
A reduced carbon footprint
The company can monitor and control its carbon footprint precisely and advance its ESG strategy
Challenge
This oil services company is based in Texas but it has significant operations throughout the USA and in global locations. In 2019, GFT offered and invested in a five-day discovery workshop that aimed to establish the transformational potential of digital technologies and data throughout the company. Specific aims were to shrink the company’s carbon footprint, reduce costs and become a data-driven business.
Although the company wanted to keep an open brief for the workshop, it already knew that equipment maintenance costs were high and increasing, accounting for around 20% of turnover. And with a maintenance schedule driven by machine failure, there could also be significant losses in production due to machine outages.
GFT saw an opportunity to implement a predictive maintenance programme to avoid catastrophic equipment failures and unscheduled maintenance. As well as making permanent cost savings, the technologies involved would empower the company to become data driven to help meet other business and ESG objectives.
The first challenge was to capture, collate and store a substantial volume of operational internet of things (IoT) data from multiple sources, including production machinery, peripheral equipment and trucks.
Engagement
GFT was invited to build a visualisation platform for IoT data and equipment monitoring. Although this would be a bespoke solution, GFT could use its proven methods to identify gaps, business risks and other digital transformation opportunities. To accelerate delivery, a minimum viable product would be built as quickly as practicable. A hybrid GFT team of 10, worked both onsite and in a several nearshore locations.
Once completed the new platform was initially applied to preventative maintenance of oil production machinery. The initial results were overwhelmingly positive. Real-time IoT data gathered from a range of sources showed that fault patterns could be detected and maintenance requirements scheduled. Within eight weeks the company made savings of circa 20% of turnover, excluding losses that would accrue to machine downtime due to catastrophic failures. Remote well-site monitoring and preventative maintenance was rolled out across all installations.
In addition to the permanent savings, this initial success proved the potential of real-time data to drive better business decisions. GFT was invited to expand the scope of its transformation programme as a foundation for machine learning (ML) predictive maintenance and root cause analysis.
The next use case related to ESG and power solutions. As a significant user of diesel in both its oilfield operations and trucks, the company wished to move to cleaner fuels, and natural gas was an obvious choice. But, to run trucks and production machines on natural gas is not easy and key metrics must be constantly monitored for both safety and compliance purposes. The new data platform offered an ideal solution, collating all the necessary metrics in real time.
So far over millions gallons of diesel have been saved. By substituting diesel with natural gas, the company is shrinking its carbon footprint, improving its ESG rating and building a path to a greener future.
With a wealth of real-time and historical data, the company was ideally prepared to adopt artificial intelligence (AI) and ML. With ML, the data model learns all the time, so detailed patterns can be established across all operations in diverse locations. As well as facilitating predictive maintenance, this provides accurate, detailed insight on how the business is running and enables comparison between operations.
One of the biggest challenges of the project was to change the organisational culture from one of "reactive" maintenance to predictive maintenance. Continued success requires persistence and the commitment of key staff to train ML models. To ensure full cooperation, GFT hosted regular staff workshops, to explain the benefits of AI and how it is much more of an opportunity than a threat.

Benefit
The new solution was delivered on time and within budget. From the outset, the data told a consistent story about operational patterns and maintenance requirements. Within six weeks, this generated a six-fold return on investment.
With its new IoT data platform this is an oil company fit for the digital age. New use cases are emerging continually and the platform has been deployed as an enterprise solution, integrated with most business processes. Total savings to date around $100 million with many more in the pipeline. The ongoing success of the solution shows that data has become the lifeblood of business across all industries.
The new data operating platform was delivered as a textbook example of GFT’s Agile methods. Every new application is built on a sustainable business case that aligns investment with quantifiable benefits.
GFT remains the company’s strategic technical partner, responsible for software development, production support and data engineering. In practice, GFT acts as an outsourced IT department with 34 FTEs. The partnership thrives on trust and transparency.
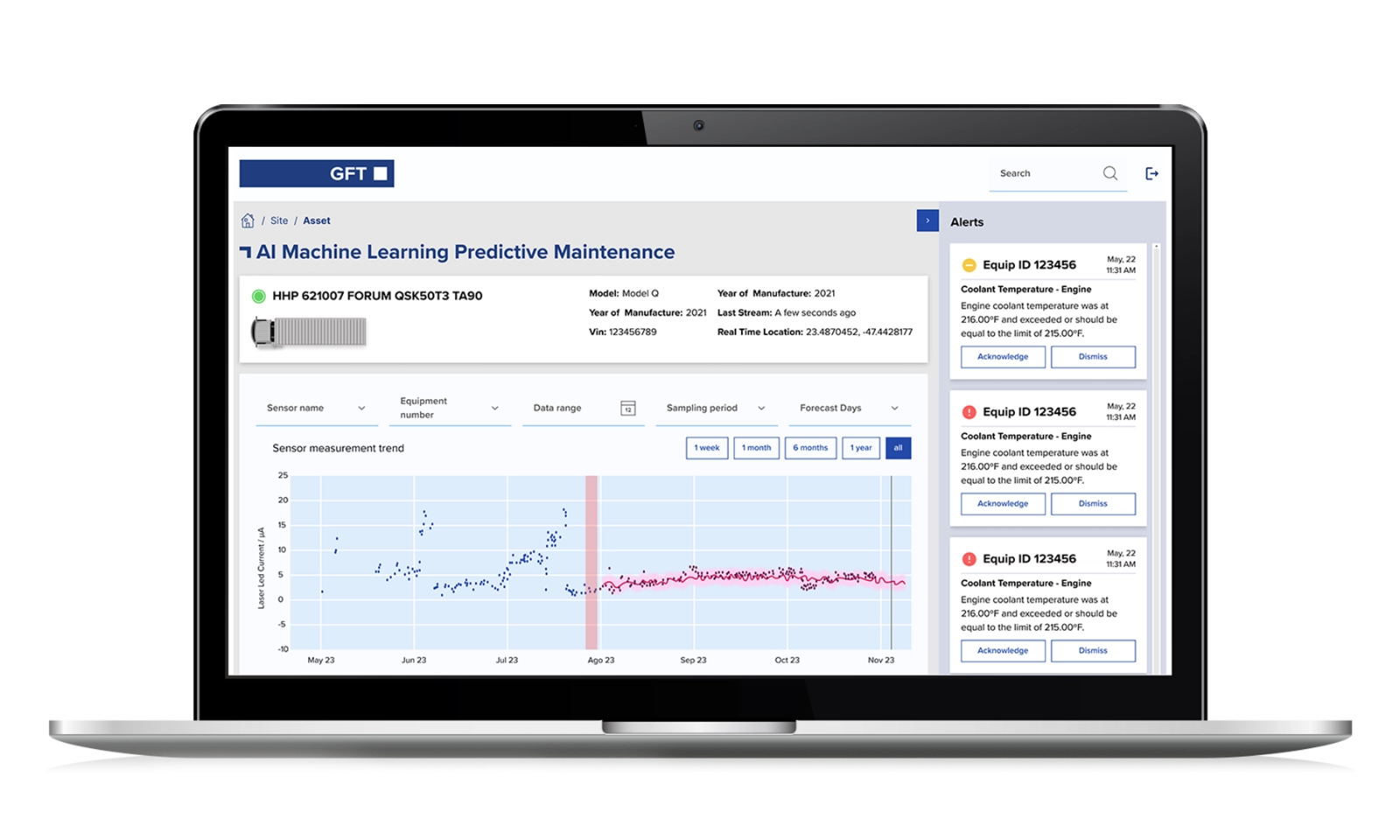
Download - just one click away
-
Success story
Data visualisation platform saves an estimated $100 million over 4 years
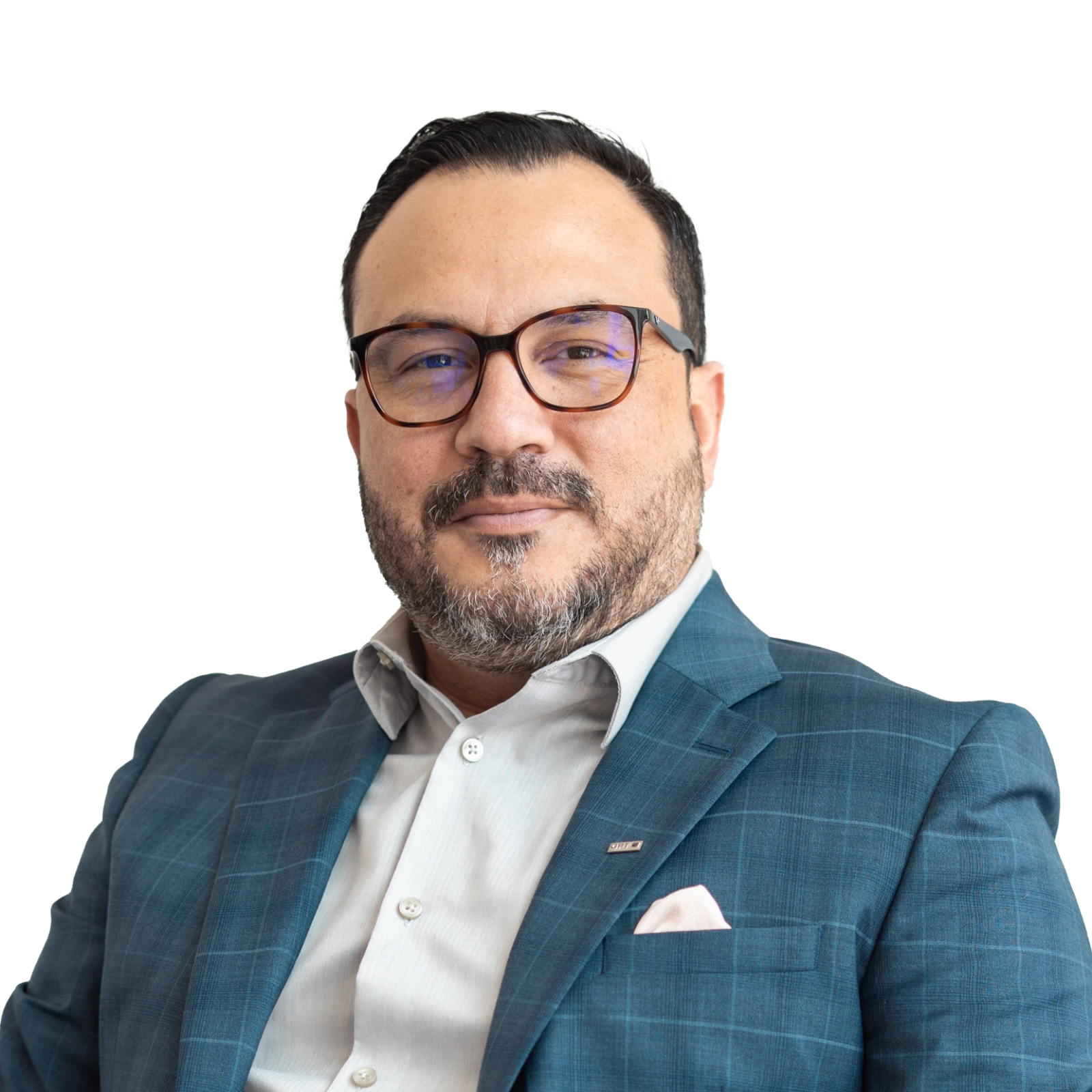