Shaping Digital Strategy in a Fast-Changing Auto Industry
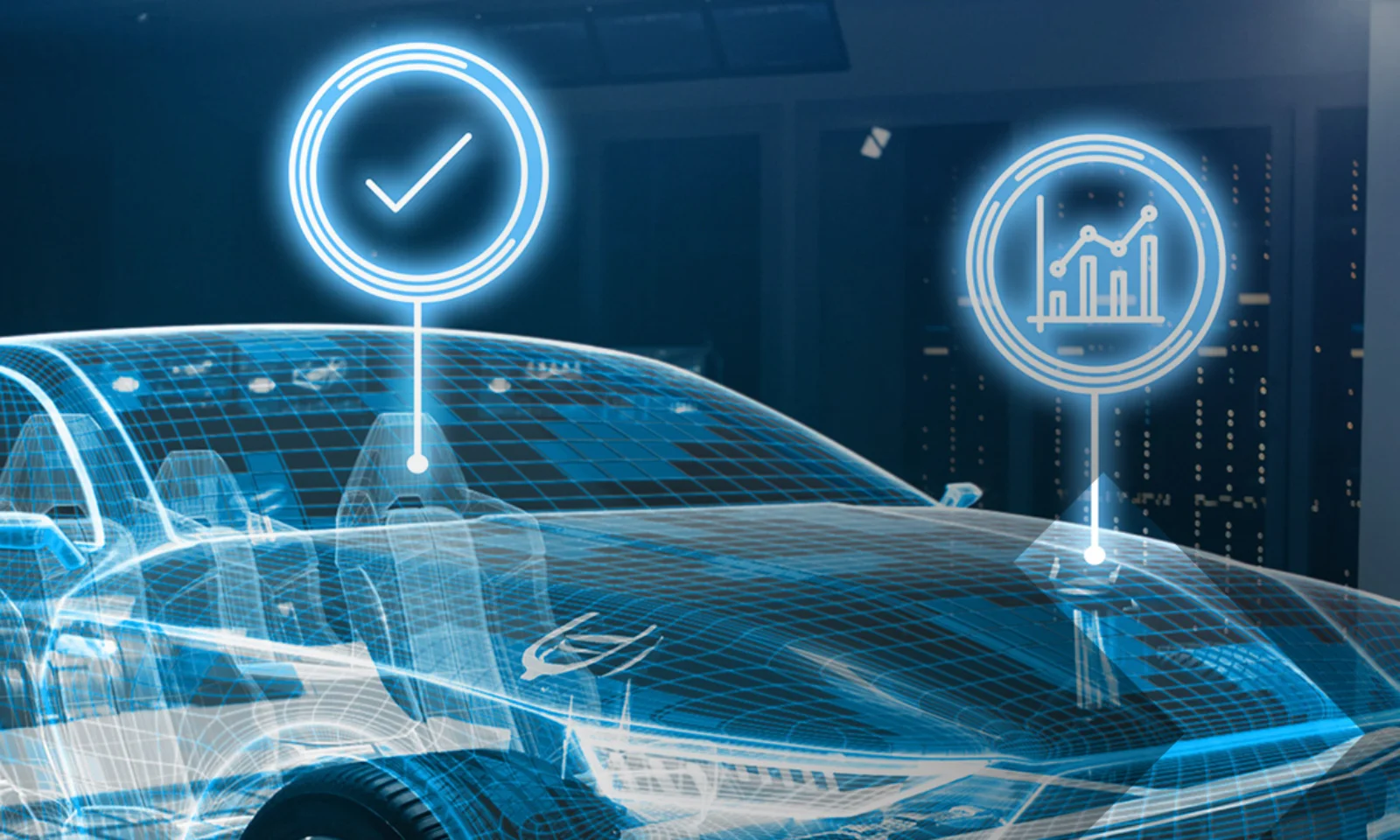
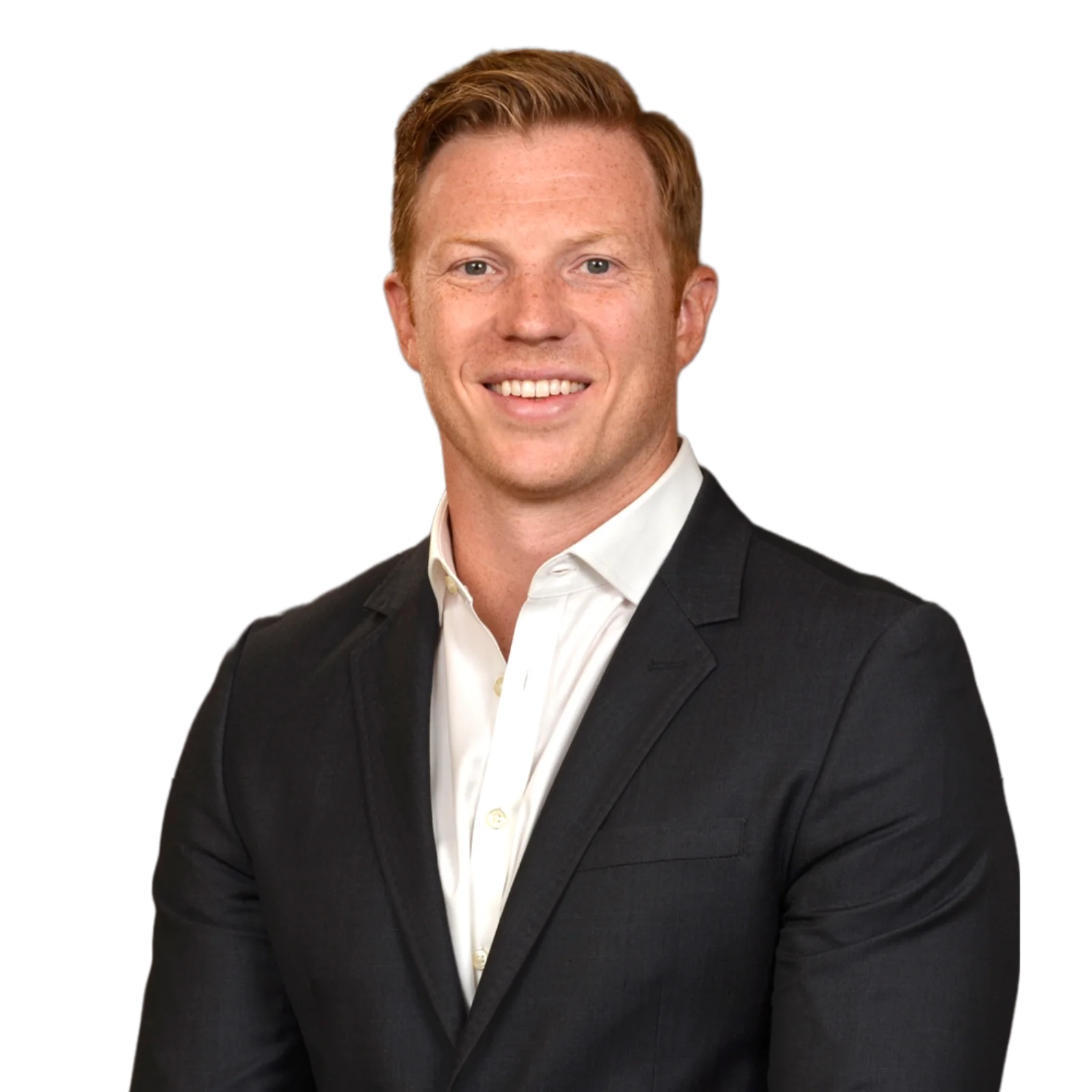
GFT US
- Batteries and electric motors are replacing internal combustion engines that have been at the heart of the industry for more than a century.
- Autonomous driving, connected cars and smart factories make it vital for vehicle manufacturers and parts suppliers to embrace new technologies and advanced IT systems—putting data in its rightful place at the center of it all.
Digital strategy has never been more important for automotive companies, and with this in mind, GFT brought together a distinguished group of technology leaders from a range of companies in the auto industry for a dinner and roundtable discussion in Detroit.
We asked participants to tell us where they are on their digital transformation journey. They described the data challenges they face. And they envisaged the IT capabilities that could help their companies deliver on the promises of a more sustainable, connected and tech-enabled auto industry. Highlights from the conversation follow.
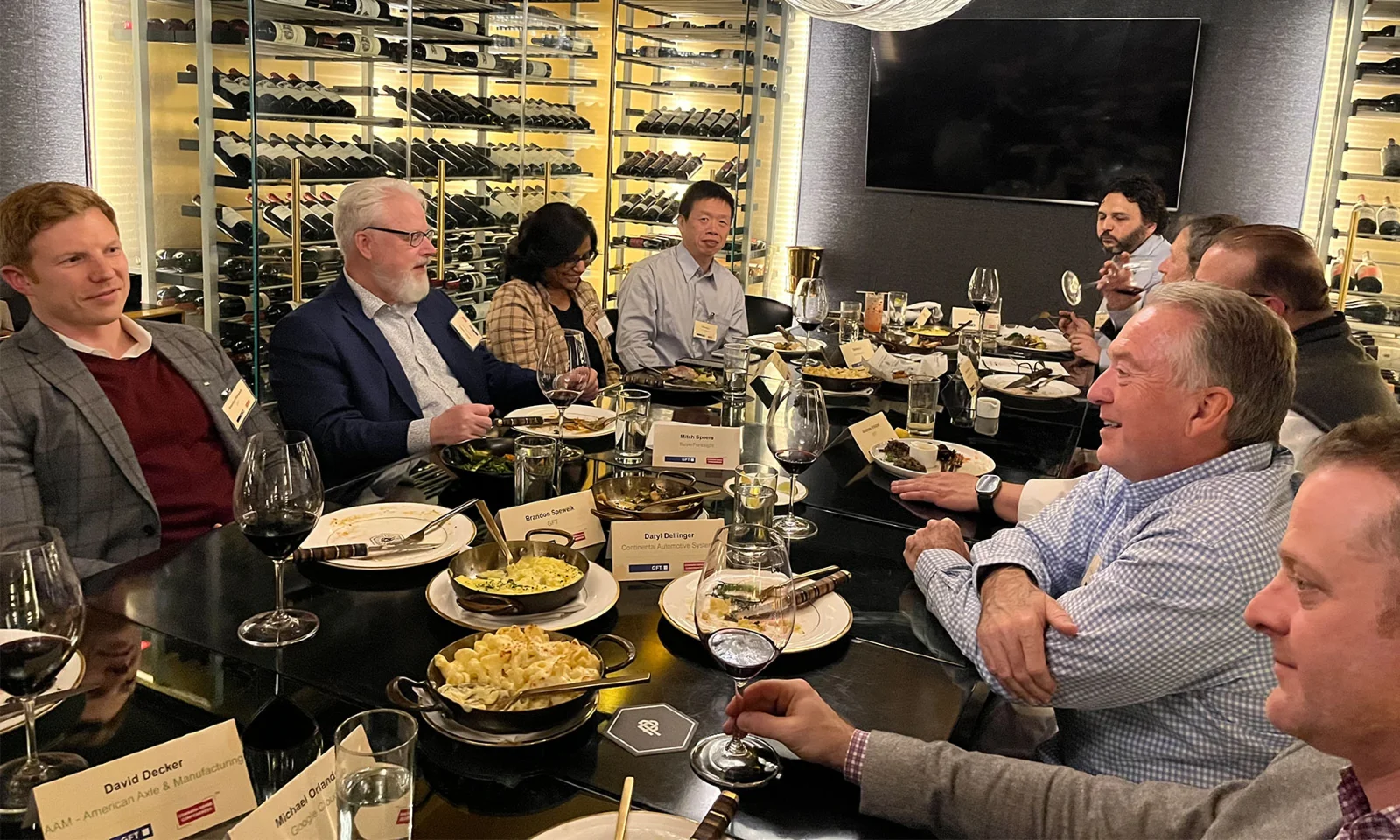
Start with better data
The discussion at the table was open and frank—and several participants conceded that the data their companies today leaves much to be desired. Needs ranged from more sensors on production lines to smarter systems to track parts inventories. Consistency in data definitions and compatibility among systems remained high on their wish lists.
One attendee, from a large parts supplier, said the organization had at least four different versions of a popular enterprise resource planning (ERP) system running at its various facilities. Despite the software originating from a single vendor, getting each of the systems to talk to one another remains difficult.
Another participant, representing a parts maker, took issue with the fact that parts and machines may be named differently from one plant to the next. The first step is a common data model to foster data coordination and consistency. “Unless we crack that nut, we’re dead in the water.”
Participants expressed hope that greater standardization will emerge to help foster more consistent data exchange ontology. One said that having a single source of truth for manufacturing data would be a boon for the industry.
Find solutions that scale
The diversity of facilities under the umbrella of a single company in the auto sector can present significant data and IT systems challenges. A tier-one parts supplier may have several hundred production sites, with individual plants sometimes answering to their own bottom line, following their own procedures and running their own IT systems. One attendee lamented, “There are probably no two facilities across my company that have the same software stack.”
Digital transformation efforts might occur in pockets, in a few plants, rather than across the entire organization. The task becomes how to find data management and automation solutions that can succeed in multiple locations—that can scale up across the entire company.
One way to approach this problem, is to look for common issues that affect a number of individual plants. “You’ve got people trying to solve the same problem over and over again,” one of our attendees said. Because there are shared challenges around inventory and demand management, for example, the implementation of a new system for these needs might create benefits in many locations.
It will always be easier to implement new technology in a pristine, newly built facility, another attendee said. A company may have some factories that are brand-new and others that are out of date, including some built from the ground-up and ones that were inherited through acquisitions. They further posited that it is important to understand and consider issues that may arise when bringing greater connectivity and smart automation to an older or less efficient facility.
Make the business case
Several people at the table made the point that digital transformation is less about some ideal end-state and more about practical steps that will improve operations, increase efficiency, lower expenses and improve the bottom line. To be sure, this is a journey, and expected future requirements must be considered, but not at the expense of making gains today. “There are things that are not being done and would have an immediate impact,” one participant said.
Communication is key. Helping people to understand the power and value of the data will help build support among employees who will be most affected by system changes—and among managers who pay for them. One piece of advice that was offered: “It can be a matter of simply saying, ‘We have been really successful with this. We have found something that is working. We think there is value to it.’”
At the same time, a digital transformation plan should always reflect the specific circumstances of individual businesses to make the case for IT spending. If there is a possibility that a plant or a unit might be sold, for example, it may make sense to avoid the expense of putting in new systems, despite a companywide effort to move towards a common data model.
“There’s a new world and a new competitive environment and a lot of new types of products and enterprises, so we are going through this transformation. The digital thread is key.”
Foster the free flow of data
Everyone at the table agreed that as technology and connectivity proliferate in vehicles, the collected data holds significant value. More plentiful data can help those in the industry better understand how a part performs over time, where a system breaks down or how drivers use or even pay for a particular feature—but only if this information gets where it needs to go in a usable form.
Benefits may be lost if an original equipment manufacturer (OEM) that controls a connected-car system fails to share data with others in the supply chain. By the same token, opportunities may be missed if a parts supplier won’t share quality control, production, inventory and other data with their automaker partners. One of the participants who works for a parts supplier commented that too often what should be an “exchange” of information feels entirely one-way. Several people at the table emphasized that building trust is vital to making this kind of information exchange succeed.
Manage the people part
Though the topics at the dinner were data and IT systems, a recurring thread in the conversation was people. Too often leadership is better at the technological challenges and less good at personnel management. Instituting a new inventory system or type of advanced automation won’t lead to desired outcomes without the trust of the people affected by the technology.
One attendee cited the implementation of machine vision technology to help monitor and improve quality on a production line. The operators working on that line weren’t ready to accept it. To build trust, managers need to be able to show employees affected by the change, a value exchange. Managers need to demonstrate how the technology can make the operator’s job better, improve someone’s career path, or make the company more successful to the benefit of everyone who works there.
